Analysis of production quality control and common faults in asphalt mixing plants
[1]. Main factors affecting the production quality of asphalt mixing plants
1. The mix ratio of asphalt concrete is incorrect
The mix ratio of asphalt mixture runs through the entire construction process of the road surface, so the scientific link between its mix ratio and production mix ratio plays an important role in production and construction. Unreasonable production mix ratio of asphalt mixture will lead to The asphalt concrete is unqualified, which affects the service life of asphalt concrete pavement and the cost control of asphalt concrete pavement.
2. The discharging temperature of asphalt concrete is unstable
The "Technical Specifications for Highway Asphalt Pavement Construction" clearly stipulates that for intermittent asphalt mixing plants, the heating temperature of the asphalt must be controlled within the range of 150-170°C, and the temperature of the aggregate must be 10-10% higher than the asphalt temperature. -20℃, the factory temperature of the mixture is generally 140 to 165℃. If the temperature does not meet the standard, flowers will appear, but if the temperature is too high, the asphalt will burn, seriously affecting the quality of road paving and rolling.
3. Mixing the mixture
Before mixing materials, the boiler model and parameters must be strictly inspected on the mixing equipment and supporting equipment to ensure that all dynamic surfaces are in good working condition. At the same time, the metering equipment must be checked regularly to ensure that the amount of asphalt and aggregates in the mixture meet the requirements of the "Technical Specifications". The production equipment of the mixing plant should be placed in a spacious place with convenient transportation conditions. At the same time, temporary waterproofing equipment, rain protection, fire prevention and other safety measures must be prepared at the site. After the mixture is mixed evenly, it is required that all mineral particles should be wrapped by asphalt, and there should be no uneven wrapping, no white matter, no agglomeration or segregation. Generally, the mixing time of asphalt mixture is 5 to 10 seconds for dry mixing and more than 45 seconds for wet mixing, and the mixing time of SMA mixture should be appropriately extended. The mixing time of the mixture cannot be reduced just to increase productivity.
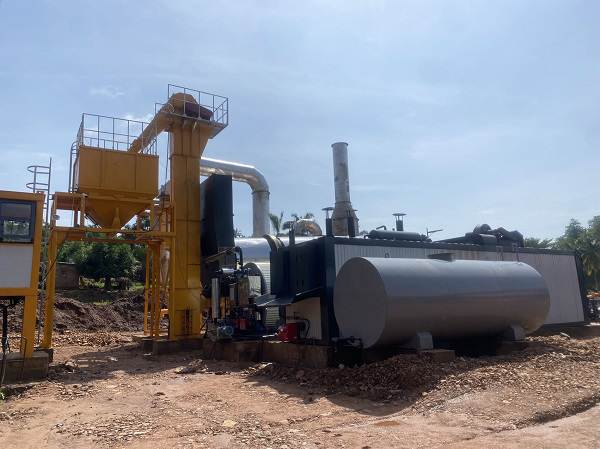

[2]. Analysis of common faults in asphalt concrete mixing plants
1. Failure analysis of cold material feeding device
Whether the variable speed belt motor or the cold material belt is stuck under something, it will have an impact on the shutdown of the variable speed belt conveyor. If the circuit of the variable speed belt conveyor fails, a detailed inspection of the frequency converter must be carried out to see if it can operate. Normally, if there is no short circuit, the conveyor belt must be checked to see if it is deviating or slipping. If it is a problem with the conveyor belt, it must be adjusted promptly and reasonably to ensure the normal operation of the function.
2. Analysis of mixer problems
Mixer problems are mainly manifested in abnormal noise during construction. At this time, we need to first consider whether the motor bracket is unstable due to the overload of the mixer. In another case, we must consider whether the bearings that play a fixed role may be damaged. This requires the workers to conduct a complete inspection, repair the bearings, and replace seriously damaged mixer parts in a timely manner to prevent the uneven surface of the mix.
3. Analysis of sensor problems
There are two situations when there are problems with the sensor. One situation is when the loading value of the silo is incorrect. At this time, the sensor needs to be checked. If the sensor fails, it must be replaced in time. The other situation is when the scale beam is stuck. If there is a problem with the sensor, I need to promptly remove the foreign matter.
4. The burner cannot ignite and burn normally.
For the problem that the incinerator cannot ignite normally when the product is heated, the operator needs to adopt the following methods to solve the problem: a comprehensive inspection of the operating room and each incineration device, such as the power supply of the transmission belt, power supply, roller, fan and other components Check in detail, then check the position of the combustion valve of the fan, check the status of the cold air door, the opening and closing status of the fan door, the status of the drying drum and the internal pressure status, whether the instrument is in manual gear mode, and all indicators are qualified. In the state, enter the second step of inspection: check whether the oil circuit is clear, whether the incineration device is normal, and whether the high-voltage package is damaged. If the problem cannot be found, go to the third step and remove the incinerator electrode. Take out the device and check its cleanliness, including whether the oil circuit is blocked by oil dirt and whether there is an effective distance between the electrodes. If the above checks are normal, then you need to conduct detailed inspection of the working status of the fuel pump. Check and test whether the pressure at the pump port meets normal conditions.
5. Analysis of abnormal negative pressure performance
The influencing factors on the internal pressure of the blower mainly include two aspects: the blower and the induced draft fan. When the blower generates positive pressure in the drum, the induced draft will generate negative pressure in the drum, and the negative pressure generated cannot be very large, otherwise dust will fly out from the four sides of the drum and affect the surrounding environment.
When negative pressure occurs in the drying drum, the staff should perform the following operations: In order to determine the performance of the damper, the air inlet of the induced draft fan must be strictly inspected. When the damper does not move, you can set it to manual operation, adjust the damper to the handwheel position, check whether it is running normally, and eliminate the situation that it is stuck. If it can be opened manually, then follow the steps Conduct detailed investigation of relevant procedures. Second, under the premise that the damper of the induced draft fan can be used normally, staff need to conduct a detailed inspection of the pulse board, check whether there are any questions about its wiring or electromagnetic switch, find the cause of the accident, and solve it scientifically in a timely manner.
6. Analysis of inappropriate oil-stone ratio
The whetstone ratio refers to the mass ratio of asphalt to sand and other fillers in asphalt concrete. It is a very important indicator for controlling the quality of asphalt concrete. If the ratio of oil to stone is too large, it will cause the "oil cake" phenomenon to appear after paving and rolling. However, if the oil-stone ratio is too small, the concrete material will diverge, resulting in rolling failure. Both situations are serious quality accidents.
7. Screen problem analysis
The main problem with the screen is the emergence of holes in the screen, which will cause the aggregates from the previous level to enter the silo of the next level. The mixture must be sampled for extraction and screening. If the whetstone of the mixture is relatively large, , the oil cake phenomenon will occur after paving and rolling the road surface. Therefore, if every period of time or an abnormality occurs in the extraction and screening data, you should consider checking the screen.
[3]. Maintenance of asphalt concrete mixing plant
1. Maintenance of tanks
The asphalt plant tank is an important device of the concrete mixing plant and is subject to serious wear and tear. Usually, the lining plates, mixing arms, blades and shaking door seals of the mixing asphalt must be adjusted and replaced in time according to the wear and tear conditions, and after each concrete mixing, the tank must be flushed in time to clean the mixing plant. The remaining concrete in the tank and the concrete attached to the material door should be thoroughly washed to prevent the concrete in the tank from solidifying. Also check frequently whether the material door opens and closes flexibly to avoid jamming of the material door. When maintaining the tank, the power supply must be disconnected, and a dedicated person must be assigned to take careful care. Before each lift, make sure there are no foreign objects in the tank, and avoid starting the main engine with load.
2. Maintenance of stroke limiter
The limiters of the asphalt concrete mixing plant include upper limit, lower limit, limit limit and circuit breaker, etc. During work, the sensitivity and reliability of each limit switch should be carefully checked frequently. The inspection content mainly includes whether the control circuit components, joints and wiring are in good condition, and whether the circuits are normal. This will have an impact on the safe operation of the mixing plant.
[4]. Asphalt mixture mixing quality control measures
1. Coarse aggregate plays a very important role in asphalt concrete. Generally speaking, gravel with a particle size of 2.36 to 25mm is generally called coarse aggregate. It is mainly used in the surface layer of concrete to reinforce the granular material, increase its friction and reduce the influencing factors of displacement. This requires that the mechanical structure of the coarse aggregate can match its needs in the field of chemical properties, so as to achieve the technical goal. needs and have specific physical properties, such as high-temperature physical performance, material density and strength influencing factors. After the coarse aggregate is crushed, the surface should remain rough, and the shape of the body should be a cube with obvious edges and corners, where The content of needle-shaped particles should be kept at a low level, and the friction inside is relatively strong. Crushed rocks with particle sizes ranging from approximately 0.075 to 2.36mm are collectively referred to as fine aggregates, which mainly include slag and mineral powder. These two types of fine aggregates have very strict cleaning requirements and are not allowed to be attached or adhered to anything. For harmful substances, the interlocking force between particles should be appropriately strengthened, and the gaps between aggregates should also be compressed to enhance the stability and strength of the material.
2. When the mixture is mixed, the mixing must be carried out strictly according to the construction temperature specified for the asphalt mixture. Before the mixing of the mixture is started every day, the temperature should be appropriately increased by 10°C to 20°C on the basis of this temperature. In this way, the asphalt mixing The quality of the materials is very beneficial. Another method is to appropriately reduce the amount of aggregate entering the drying barrel, increase the temperature of the flame, and ensure that when starting the mixing, the heating temperature of the coarse and fine aggregates and asphalt is slightly higher than the specified value, this can effectively prevent the asphalt concrete mixing pan from being discarded.
3. Before construction work is carried out, the gradation review of aggregate particles must first be done. This review process is very important and directly affects the construction quality of the project. Under normal circumstances, there is often a big difference between the actual proportion and the target proportion. In order to better make the actual proportion consistent with the target proportion, it is necessary to make good adjustments in terms of the motor rotation speed of the hopper and the feeding flow rate. , to better ensure consistency and thereby better achieve the matching effect.
4. At the same time, the screening capacity of the screen affects the setting of the half and floor output to a certain extent. In the case of less experience, if you want to do a good job in screen screening, you must set different output speeds. to fulfill. In order to ensure the normal production of geotextiles and ensure that there is no large error in the grading of mineral materials, the mineral materials must be proportioned according to the expected output before construction, and the production parameters must be balanced with the set parameters. , so that it does not change during the construction process.
5. On the basis of ensuring the normal use of asphalt mixture, it is necessary to set the actual usage amount of specific aggregates and mineral powder, and at the same time appropriately reduce the usage amount of mineral powder; secondly, pay attention to not being able to use it during the mixing construction process. Change the size of the damper, and assign professional staff to conduct regular inspections to ensure that the thickness of the asphalt membrane meets the construction requirements, prevent the mixture from showing a whitish color, and improve the quality of construction.
6. The mixing time and mixing temperature of the mixture must be strictly controlled. The uniformity of the asphalt mixture has a very close relationship with the length of the mixing time. The two are directly proportional, that is, the longer the time, the more uniform it will be. However, if the time is not controlled well, the asphalt will age, which will affect the quality of the mixture. adversely affect the quality. Therefore, the temperature must be scientifically controlled during mixing. The mixing time of each plate of the intermittent mixing equipment is controlled between 45-50 seconds, while the dry mixing time should be longer than 5-10 seconds, depending on the mixing time of the mixture. Stir evenly as standard.
In short, as a mixing plant staff in the new era, we must be fully aware of the importance of strengthening the quality and maintenance of asphalt mixing equipment. Only by controlling the quality of asphalt mixing plants well can we ensure the asphalt mixing Only by improving the quality of mix plant production can we produce more high-quality and efficient asphalt mixtures, laying a solid foundation for improving project quality.