With the rapid development of my country's national economy, the traffic volume is also increasing day by day, which makes highway construction face severe tests, which raises new topics for the maintenance and management of asphalt pavement. The quality of asphalt concrete and its paving can directly affect the quality of the road surface. This article mainly takes the LB-2000 asphalt mixing plant as an example, starting with its working principle, and analyzes the causes of failures in the asphalt mixing plant in detail, further discusses the specific preventive measures, and proposes relevant preventive measures in order to Provide an effective theoretical basis for the normal operation of asphalt mixing plants.
Working principle of intermittent mixing plant
The working principle of the LB-2000 asphalt mixer plant is: (1) First, the central control room issues a start-up command. After receiving the relevant command, the cold material in the cold material bin transports the relevant materials (aggregate, powder) to the dryer through the belt conveyor. It is dried in the drum, and after drying, it is transported to the vibrating screen through a hot material elevator and screened. (2) Transport the screened materials to different hot material bins. The relevant weight values ??of each chamber door are measured using electronic scales, and then placed into the mixing tank. Then the hot asphalt is weighed and sprayed into the mixing tank. Inside. (3) Fully stir the various mixtures in the mixing tank to form finished materials and transport them to the bucket truck. The bucket truck transports the finished materials through the track, unloads the finished materials into the storage tank, and puts them on the transport vehicle through the discharge gate.
The steps of conveying, drying, screening and other steps in the work process of an asphalt mixing plant are carried out in one go, without any pauses in between. The process of mixing, weighing and finished materials of various materials is cyclical.
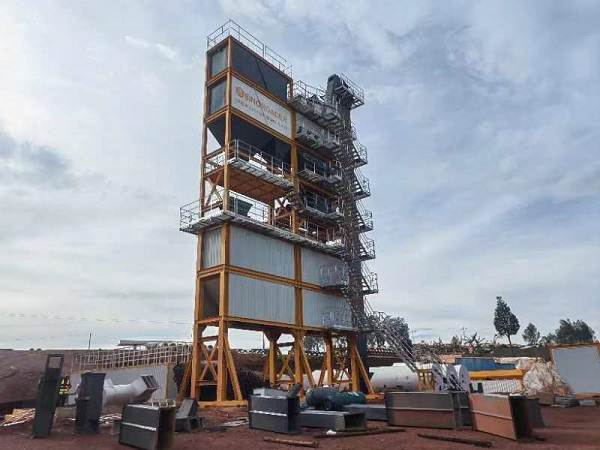
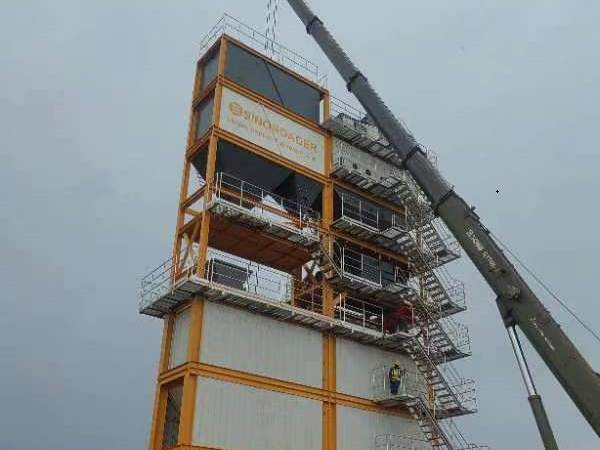
Failure analysis of intermittent mixing plant
Based on relevant practical experience, this article summarizes and analyzes the related causes of failures in the asphalt mix plant, and proposes solutions related to the boiler principle. There are many reasons for equipment failure. This article mainly explains some of the main reasons, which mainly include the following aspects:
Mixer failure
An instantaneous overload of the mixer may cause the fixed support of the drive motor to become dislocated, causing the sound produced by the mixer to be different from normal conditions. At the same time, damage to the fixed shaft may also cause abnormal sound. In this case, it is necessary to reposition, fix or replace the bearing to solve the problem. At the same time, if the blades, mixing arms and related equipment are severely worn or fallen off during operation, they should be replaced immediately, otherwise uneven mixing will occur and the quality of the finished materials will be seriously affected. If an abnormal temperature is found in the mixer discharge, it is necessary to check and clean the temperature sensor and verify whether it can work normally.
Cold material feeding device failure
The failure of the cold material feeding device has the following aspects: (1) If there is too little material in the cold hopper, it will have a direct and serious impact on the belt conveyor during the loading of the loader, which will cause it to The overload phenomenon forces the variable speed belt conveyor to shut down. In order to solve this problem, it is necessary to ensure that there are enough pellets in each cold hopper at all times; (2) If the variable speed belt motor fails during operation It will also cause the variable speed belt conveyor to stop. In this case, you should first check the motor's control inverter, and then check whether the circuit is connected or open. If there is no fault in the above two aspects, you should check whether the belt is slipping. If it is a problem with the belt, it should be adjusted so that it can operate normally; (3) Abnormal function of the variable speed belt conveyor may also be caused by gravel or foreign objects stuck under the cold material belt. In view of this, In this case, manual troubleshooting should be carried out to ensure the operation of the belt; (4) The failure of the corresponding control inverter in the control cabinet is also one of the reasons for the abnormal function of the variable speed belt conveyor, and it should be repaired or replaced; (5) Each belt conveyor shuts down abnormally It cannot be ruled out that it is usually caused by accidentally touching the emergency stop cable and just reset it.
Asphalt concrete discharge temperature is unstable
In the process of producing asphalt concrete, there are very high requirements for temperature, which should not be too high or too low. If the temperature is too high, it will easily cause the asphalt to "scorch", and if the temperature is too low, it will cause If the adhesion between sand and gravel materials and asphalt is uneven, the finished product will have no use value and can only be discarded, causing inestimable losses.
Sensor failure
When the sensor fails, the feeding of each silo will be inaccurate. This phenomenon should be checked and replaced in time. If the scale beam is stuck, it will cause sensor failure and foreign matter should be removed.
When the mineral material is heated, the burner cannot ignite and burn normally.
If the burner fails to ignite and burn normally when heating mineral materials, the following steps should be followed: (1) First check whether the ignition and combustion conditions inside the operating room meet the relevant requirements, including blowers, belts, electric fuel pumps, drying drums, Observe the power on and off of the induced draft fan and other equipment, and then check whether the induced draft fan damper and the cold air door are closed at the ignition position, and whether the selector switch, drying drum and internal pressure detection instrument are in manual mode. position and manual status. (2) If the above factors do not affect the ignition condition, the initial ignition condition, fuel condition and fuel passage obstruction should be checked, and then the burner ignition motor ignition condition and high-pressure package combustion damage should be checked. If they are all normal, check again. Check whether the electrodes have excessive oil stains or excessive distance between electrodes. (3) If all the above are normal, you should check the operation of the fuel pump, check the outlet pressure of the pump oil, and check whether it can meet the requirements and the closing condition of the compressed air valve.
Negative pressure is abnormal
The atmospheric pressure in the drying drum is negative pressure. The negative pressure is mainly affected by the blower and induced draft fan. The blower will generate positive pressure in the drying drum. The dust in the drying drum will fly out of the drum when affected by the positive pressure. out and cause environmental pollution; the induced draft will generate negative pressure in the drying drum. Excessive negative pressure will cause cold air to enter the drum, causing a certain amount of heat energy, which will greatly increase the amount of fuel used and increase the cost. The specific solutions when positive pressure is formed in the drying drum are: (1) Check the status of the induced draft fan damper, turn the induced draft damper control and rotate the damper to the manual and handwheel, and then check the closing status of the damper. Check if the damper bearing is damaged and the blade is stuck. If it can be opened manually, it can be determined that the fault is in the electric actuator and actuator, and the problem can be solved by performing relevant troubleshooting. (2) When the induced draft fan damper can operate, it is necessary to check the closing condition of the pulse puller on the upper part of the dust removal box, the operating status of the control circuit, solenoid valve and air path, and then find out the source of the fault and eliminate it.
Whetstone ratio is unstable
The ratio of the quality of asphalt to the quality of sand and other filling materials in asphalt concrete is the whetstone ratio. As an important indicator to control the quality of asphalt concrete, its value directly affects the quality of asphalt concrete. A stainless steel chain with a stone-to-stone ratio that is too small or too large will cause serious quality accidents: an oil-stone ratio that is too small will cause the concrete material to diverge and be rolled out of shape; an oil-stone ratio that is too large will cause "oil cake" to form on the pavement after rolling. .
Conclusion
Analysis of common faults of intermittent mixing plants in order to achieve a more complete, effective and reasonable performance in actual work. No part of it can be ignored or overemphasized when handling faults. This is the only way The quality of the finished product will be of reasonable standard. The quality operation of a good mixing plant can effectively ensure the quality of the project, and is also conducive to cost reduction and improvement of construction efficiency.