Discussion on the modification of dust removal equipment in asphalt concrete mixing plant
Asphalt concrete mixing station (hereinafter referred to as asphalt plant) is an important equipment for high-grade highway pavement construction. It integrates various technologies such as machinery, electrical, and concrete foundation production. At present, in the construction of infrastructure projects, people's awareness of environmental protection has increased, energy conservation and emission reduction are advocated, and awareness of repairing old and recycling waste has increased. Therefore, the performance and condition of the dust removal equipment in the asphalt plants are not only directly related to the quality of the finished asphalt mixture. Quality, and puts forward higher requirements for the technical level of equipment manufacturers' designers and the operation and maintenance awareness of equipment users.
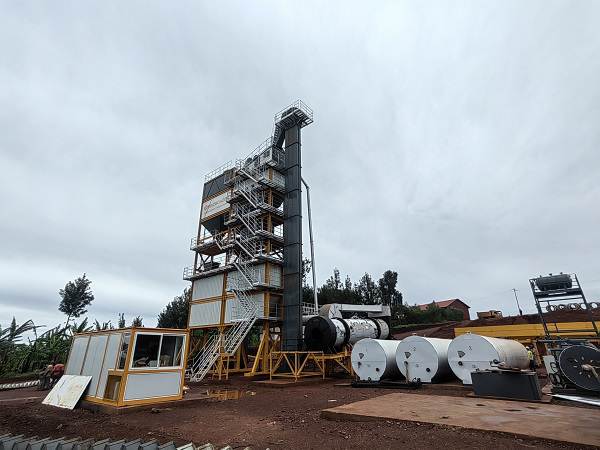
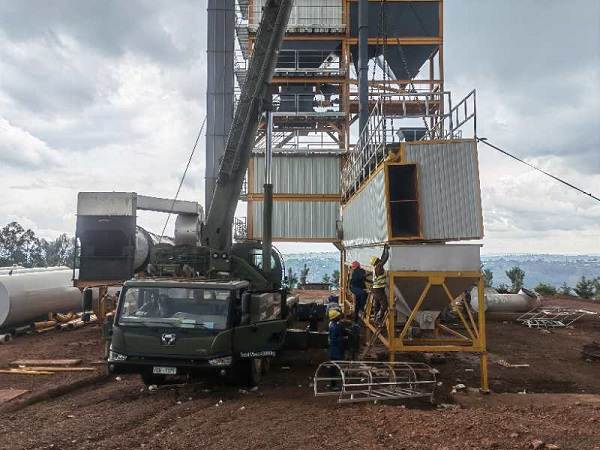
[1]. Structure and principle of dust removal equipment
This article takes the Tanaka TAP-4000LB asphalt plant as an example. The overall dust removal equipment adopts the belt dust removal method, which is divided into two parts: gravity box dust removal and belt dust removal. The control mechanical mechanism is equipped with: exhaust fan (90KW*2), servo motor controlled air volume regulating valve, belt dust collector pulse generator and control solenoid valve. The auxiliary executive mechanism is equipped with: chimney, chimney, air duct, etc. The dust removal cross-sectional area is about 910M2, and the dust removal capacity per unit time can reach about 13000M2/H. The operation of dust removal equipment can be roughly divided into three parts: separation and dust removal-circulation operation-dust exhaust (wet treatment)
1. Separation and dust removal
The exhaust fan and servo motor air volume control valve form negative pressure through the dust particles of the dust removal equipment. At this time, the air with dust particles flows out at high speed through the gravity box, bag dust collector (the dust has been removed), air ducts, chimneys, etc. Among them, the dust particles larger than 10 microns in the tube condenser fall freely to the bottom of the box when they are dusted by the gravity box. The dust particles smaller than 10 microns pass through the gravity box and reach the belt dust collector, where they are bonded to the dust bag and are sprayed by pulsed high-pressure airflow. Fall on the bottom of the dust collector.
2. Cycle operation
The dust (large particles and small particles) that falls at the bottom of the box after dust removal flows from each screw conveyor into the zinc powder metering storage bin or recycled powder storage bin according to the actual production mix ratio.
3. Dust removal
The recycled powder flowing into the recycled powder bin is dust-exhausted and recovered by the wet treatment mechanism.
[2]. Problems existing in the use of dust removal equipment
When the equipment was running for about 1,000 hours, not only high-speed hot air flow came out of the dust collector chimney, but also a large amount of dust particles were entrained, and the operator found that the cloth bags were seriously clogged, and a large number of cloth bags had holes. There are still some blisters on the pulse injection pipe, and the dust bag must be replaced frequently. After technical exchanges between technicians and communication with Japanese experts from the manufacturer, it was concluded that when the dust collector left the factory, the dust collector box was deformed due to defects in the manufacturing process, and the porous plate of the dust collector was deformed and was not perpendicular to the air flow injected by the blow pipe, causing deviation. The oblique angle and individual blisters on the blow pipe are the root causes of the bag being broken. Once it is damaged, the hot air flow carrying dust particles will directly pass through the dust bag-flue-chimney-chimney-atmosphere. If thorough rectification is not carried out, it will not only greatly increase the equipment maintenance costs and production costs invested by the enterprise, but also reduce production efficiency and quality and seriously pollute the ecological environment, creating a vicious cycle.
[3]. Transformation of dust removal equipment
In view of the above serious defects in the asphalt mixer plant dust collector, it must be thoroughly renovated. The focus of the transformation is divided into the following parts:
1. Calibrate the dust collector box
Since the perforated plate of the dust collector has been severely deformed and cannot be completely corrected, the perforated plate must be replaced (with an integral type instead of a multi-piece connected type), the dust collector box must be stretched and corrected, and the supporting beams must be completely corrected.
2. Check some control components of the dust collector and carry out repairs and modifications
Conduct a thorough inspection of the pulse generator, solenoid valve, and blow pipe of the dust collector, and do not miss any potential fault points. To check the solenoid valve, you should test the machine and listen to the sound, and repair or replace the solenoid valve that does not act or acts slowly. The blow pipe should also be carefully inspected, and any blow pipe with blisters or heat deformation should be replaced.
3. Check the dust bags and sealed connection devices of dust removal equipment, repair old ones and recycle them to save energy and reduce emissions.
Inspect all dust removal bags of the dust collector, and adhere to the inspection principle of "not letting go of two things". One is not to let go of any damaged dust bag, and the other is not to let go of any clogged dust bag. The principle of "repair the old and reuse the waste" should be adopted when repairing the dust bag, and should be repaired based on the principles of energy saving and cost saving. Carefully check the sealing connection device, and repair or replace damaged or failed seals or rubber rings in a timely manner.