1. Disassembly, assembly and transportation guidelines
The disassembly and assembly work of the mixing station implements a division of labor responsibility system, and relevant plans are formulated and implemented to ensure that the entire process of disassembly, hoisting, transportation and installation is safe and accident-free. At the same time, we should implement the principles of first small before large, easy first before difficult, first ground before high altitude, first peripheral then host, and who disassembles and who installs. In addition, the degree of equipment collapse should be properly controlled to meet the lifting and transportation requirements while maintaining equipment installation accuracy and operational performance.
2. The key of disassemble
(1) Preparation work
Since the asphalt station is complex and large, a practical disassembly and assembly plan should be formulated based on its location and actual on-site conditions before disassembly and assembly, and a comprehensive and specific safety skills briefing should be conducted for the personnel involved in the disassembly and assembly.
Before disassembling, the appearance of the asphalt station equipment and its accessories should be inspected and registered, and the mutual orientation of the equipment should be mapped for reference during installation. You should also work with the manufacturer to cut off and remove the power, water and air sources of the equipment, and drain the lubricating oil, coolant and cleaning fluid.
Before disassembly, the asphalt station should be marked with a consistent digital identification positioning method, and some symbols should be added to the electrical equipment. Various disassembly symbols and signs must be clear and solid, and positioning symbols and positioning scale measurement points should be marked at relevant locations.
(2) The process of disassemble
All wires and cables must not be cut. Before disassembling the cables, three comparisons (internal wire number, terminal board number, and external wire number) must be made. Only after confirmation is correct can the wires and cables be disassembled. Otherwise, the wire number markings must be adjusted. The removed threads should be firmly marked, and those without marks should be patched up before being dismantled.
In order to ensure the relative safety of the equipment, appropriate machines and tools should be used during disassembly, and destructive disassembly is not allowed. The removed bolts, nuts and positioning pins should be oiled and immediately screwed or inserted back into their original positions to avoid confusion and loss.
The disassembled parts should be cleaned and rust-proofed in time, and stored at the designated address. After the equipment is disassembled and assembled, the site and waste must be cleaned up in time.

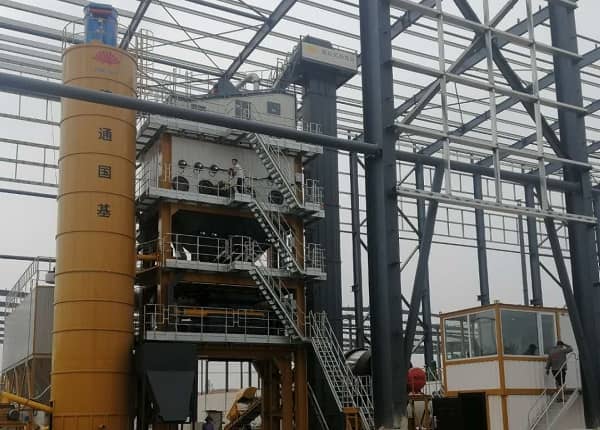
3. The key of lifting
(1) Preparation work
Establish an asphalt station equipment transition and transportation team to organize the transition and transportation division of labor, propose safety skill requirements for hoisting and transportation operations, and formulate a hoisting plan. Examine the transfer transportation route and understand the distance of the transfer transportation highway and the super-high and ultra-wide restrictions on the road sections.
Crane drivers and lifters must hold special operation certificates and have more than three years of working experience. The tonnage of the crane should meet the requirements of the hoisting plan, have complete license plates and certificates, and pass the inspection by the local technical supervision department. Slings and spreaders meet the requirements and pass the quality inspection. The transport equipment should be in good condition, and the license plates and certificates should be complete and qualified.
(2) Lifting and hoisting
Safety operating procedures should be strictly followed during the lifting process. On-site hoisting operations must be directed by a dedicated crane worker, and multiple people must not be directed. At the same time, we will equip full-time safety inspectors to eliminate unsafe factors in a timely manner.
Intermittent lifting operations should be avoided. In order to avoid damaging the equipment during hoisting, appropriate lifting points should be selected and lifted slowly and with care. Protective measures should be taken where the wire rope comes into contact with the equipment. Riggers must wear safety helmets and safety belts when operating at high altitudes, and their use must comply with safety regulations.
Equipment that has been loaded onto the trailer should be fastened with sleepers, triangles, wire ropes and manual chains to prevent it from falling during transportation.
(3) Transit transportation
During transportation, a safety assurance team consisting of 1 electrician, 2 line pickers and 1 safety officer should be responsible for transportation safety during transportation. The safety assurance team should be equipped with necessary tools and equipment to clear the way in front of the transport convoy. Number the fleet before departure and proceed in numbered order during the journey. When transporting equipment that cannot be collapsed and whose volume exceeds the specified value, significant signs must be set up at the excess area, with red flags hung during the day and red lights hung at night.
During the entire road section, the tow truck driver should follow the instructions of the safety assurance team, abide by road traffic laws, drive cautiously, and ensure driving safety. The safety assurance team should check whether the equipment is tightly bundled and whether the vehicle is in good condition. If any unsafe hazard is found, it should be eliminated immediately or contact the commanding officer. It is not allowed to drive with malfunctions or safety hazards.
Do not follow the vehicle too closely while the convoy is moving. On ordinary highways, a safe distance of about 100m should be maintained between vehicles; on highways, a safe distance of about 200m should be maintained between vehicles. When a convoy passes a slow vehicle, the driver of the passing vehicle must be responsible for reporting the road conditions ahead to the vehicle behind and guiding the vehicle behind to pass. Do not forcefully overtake without clearing the road conditions ahead.
The fleet can choose a suitable place to rest temporarily according to the driving conditions. When temporarily stopped in traffic jams, asking for directions, etc., the driver and passengers of each vehicle are not allowed to leave the vehicle. When a vehicle is temporarily stopped, it needs to turn on its double flashing lights as a warning, and other vehicles have the responsibility to remind the driver to choose an appropriate driving speed.
4. The key of installation
(1) Basic settings
Prepare the location according to the floor plan of the equipment to ensure smooth entry and exit for all vehicles. The anchor bolts of the legs of the mixing equipment building should be able to move appropriately in the foundation holes to adjust the position of the legs. Use appropriate lifting equipment to place the outriggers in place, and install the connecting rods to the tops of the outriggers. Pour mortar into the foundation hole. After the cement hardens, place the washers and nuts on the anchor bolts and tighten the legs in place.
(2) Equipment and devices
To install the bottom platform, use a crane to lift the bottom platform of the building so that it falls on the outriggers. Insert the positioning pins on the outriggers into the corresponding holes in the bottom plate of the platform and secure the bolts.
Install the hot material elevator and lift the hot material elevator to a vertical position, then place its bottom on the foundation and install the support rods and bolts to prevent it from swinging and rotating. Then align its discharge chute with the connection port on the dust sealing cover of the vibrating screen.
Install the drying drum. Lift the drying drum into place and install the legs and support rods. Open the dust sealing cover on the hot material elevator, and connect the discharge chute of the drying drum with the feed chute of the hot material elevator. By adjusting the height of the elastic legs at the feed end of the drying drum, the tilt angle of the drying drum is adjusted in place. Lift the burner to the installation flange and tighten the installation bolts, and adjust it to the correct position.
Install the skewed belt conveyor and vibrating screen and hoist the skewed belt conveyor in place so that it is connected with the feed trough of the drying drum. When installing the vibrating screen, its position should be corrected to prevent the material from deflecting, and ensure that the vibrating screen is tilted at the required angle in the length direction.
To install each component of the asphalt system, hoist the asphalt pump with an independent chassis into place, connect the device to the asphalt insulation tank and the mixing equipment body, and install a discharge valve at the lower point of the asphalt pump inlet pipeline. The asphalt transportation pipeline should be installed at an angle, and its inclination angle should be no less than 5° so that the asphalt can flow smoothly. When installing asphalt pipelines, their height should ensure smooth passage of vehicles underneath them.
The asphalt three-way valve is located above the asphalt weighing hopper. Before installation, remove the cock on the valve, insert a rod-shaped smooth seal into the valve body, put it back and tighten the cock.
The wiring and installation of electrical equipment must be performed by qualified electricians.
5. The key of storage
If the equipment needs to be shut down for a long time for storage, the location should be planned and leveled before storage to keep the incoming and outgoing routes clear.
Before storing the equipment, the following work should be done as needed: remove rust, bundle and cover the equipment, as well as inspect, inspect, store and protect all construction machinery, testing instruments, cleaning equipment and labor protection supplies; empty the mixing equipment All materials inside; cut off the power supply to prevent the equipment from starting accidentally; use protective tape to tie the V-shaped tape, and use grease to coat the transmission chain and adjustable bolts;
Protect the gas system according to the requirements of the gas system instructions; cover the outlet of the drying drum exhaust chimney to prevent rainwater from flowing in. During the equipment storage process, a dedicated person should be designated to supervise the equipment, perform regular cleaning and maintenance, and keep records.