How to be a qualified asphalt mixing plant operator? First of all, the operator should be proficient in the structure and working principles of each part of the mixing station. On this basis, strictly control all production details, especially the metering system, because the quality of the metering work will directly affect the quality of the asphalt mixture. Technical indicators.
Regarding the stone measurement system, it should be noted that:
(1) Keep each discharge door open and close flexibly and quickly;
(2) Each discharge port should be kept clear and free of sediment to ensure that the stone can flow down quickly and evenly during measurement;
(3) Each discharge door must be closed promptly and well sealed. There must be no leakage of material at the end of single material measurement;
(4) The area around the aggregate weighing hopper must be kept clean and there must be no foreign matter to avoid jamming the hopper. The aggregate weighing hopper must be kept completely suspended at all times;
(5) The preload of each aggregate load cell should be balanced, the force should be consistent, and the induction should be sensitive.
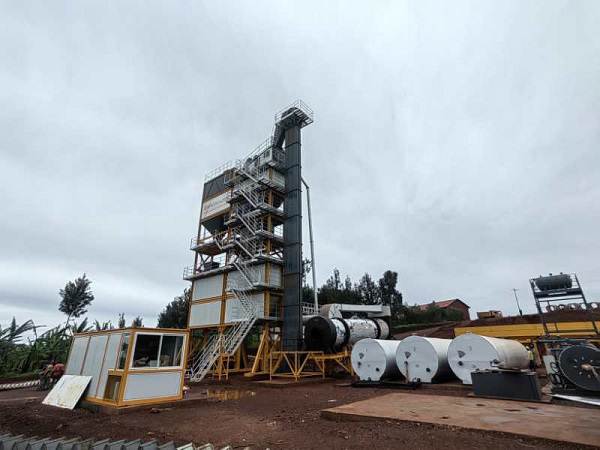
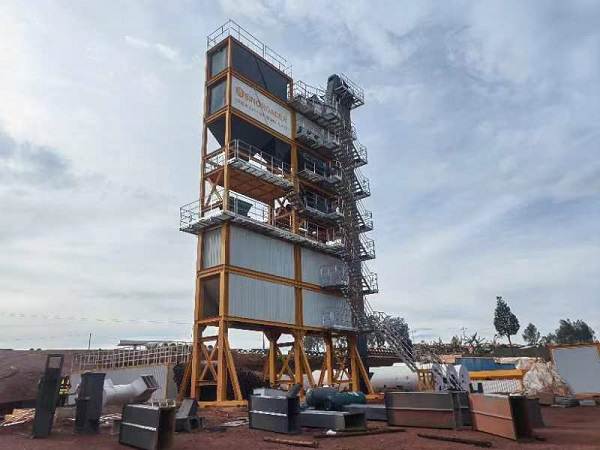
For powder metering systems, the following points should be noted:
(1) Keep the powder conveying pipeline smooth and without any blockage;
(2) The feeder or valve must be tightly sealed and no powder shall leak when the measurement is completed;
(3) Frequently remove dust and debris on the powder metering hopper to keep it clean;
(4) The entire metering system must be well sealed to prevent the powder from getting damp and clumping;
(5) The powder scale must be discharged thoroughly, and there must be no residual powder inside the scale. The discharge door must be closed tightly, and no powder should leak during measurement.
Pay attention to the following for asphalt metering systems:
(1) Before starting production, the pipeline must be fully heated to ensure that the asphalt temperature in the system reaches the specified value;
(2) The asphalt spraying pipe must be clean and smooth, and the nozzle part must not be blocked, otherwise the spraying will be uneven and the mixing effect will be affected;
(3) The asphalt spray pump or opening valve must be closed tightly to ensure that there is no dripping after the asphalt spraying is completed;
(4) The action of the asphalt metering switching valve must be accurate and timely, and the sealing must be good. The asphalt metering barrel must be hung firmly and flexibly.
For the entire metering system of the asphalt mixing plant, the operator must check it frequently. Check whether each weighing scale is completely suspended and whether there is any sticking phenomenon. Check whether each weighing sensor is working normally and whether the induction is sensitive. Verify regularly to make the displayed value consistent with the actual value. If any problem is found, solve it in time to ensure that the measurement system is always in good working condition.
Secondly, the operator should accumulate rich experience and be able to foresee most mechanical failures and solve and eliminate hidden dangers as soon as possible. After a fault occurs, it should be accurately judged and eliminated in time to ensure the normal use of the machine. To achieve this, in addition to maintaining the machinery in a timely manner according to regulations, the operator must also do the following:
(1) The operator should patrol frequently, observe carefully, and carefully inspect frequently moved parts. Check whether the connections are loose, whether the lubrication is good, whether the movement is flexible, whether there is abnormal wear, etc., and deal with any problems in a timely manner;
(2) When the mixing station is rotating, listen with your ears, think with your heart, and understand every sound. If there are any abnormal sounds. It is necessary to find out the cause and deal with it properly;
(3) Be good at identifying various smells. For example, if the oil temperature is too high, the discharge temperature exceeds the limit, circuits and electrical appliances are short-circuited and burned out, overheating caused by abnormal friction, electrical appliances and circuits are overloaded and cause serious heating, etc., they will emit different smells. Through different smells, Partial failures can also be anticipated.
In short, the operator should pay attention to the appearance and color, use various senses and use different instruments to understand every abnormal change, analyze it carefully, find out the reasons, and find out the hidden dangers. Due to the complex structure of the mixing station, there are many types of components, including electrical and gas control systems, asphalt supply systems, combustion systems, metering systems, dust removal systems, etc. It is very difficult for an operator to master all parts and accurately judge and eliminate all faults in a short period of time. Therefore, if you want to be a good operator, you must observe carefully, think frequently, summarize carefully, and constantly accumulate experience. In addition, in addition to being proficient in equipment, operators should also have knowledge of product quality control. That is to say, they are familiar with the temperature, oil-stone ratio, gradation, etc. of the asphalt mixture, and can make technical judgments on the mixture with skill, and analyze and solve problems in the mixture in a timely manner.
(1) Temperature control of the mixture:
The temperature of the mixture is one of the criteria for the qualification assessment of the mixture. If the temperature is too high or too low, it will be waste and cannot be used. Therefore, how to control temperature is one of the basic skills that operators should possess.
Factors that affect mixture temperature include fuel quality. If the quality of the fuel is poor, the calorific value is low, and the combustion is insufficient, it will cause the stone to be heated unstable, the temperature will be low, and the combustion residue will remain in the mixture, seriously affecting the quality of the mixture. If the fuel viscosity is too high, the impurity content is high, and the water content is high. It will cause ignition difficulties, pipe blockage, and temperature control. The moisture content of the raw materials is another factor that affects the temperature. The raw material has a large moisture content and is uneven. During the production process, the heating temperature of the stone is difficult to control. In addition, the technical condition of the combustion system, the pressure of the fuel supply pump, and the amount of fuel injection are all related to the temperature of the mixture. Failures such as wear, air leakage, and blockage of the combustion system prevent each component from maintaining its original performance, resulting in low system pressure, unstable fuel supply, poor atomization combustion effect, and seriously affecting the stirring temperature.
Therefore, experienced operators should be able to accurately judge the quality of fuel, the dryness and wetness of raw materials, and the working condition of the combustion system. Take appropriate measures promptly when problems are discovered. Although today's mixing equipment has automatic temperature control capabilities, the temperature control has a lag because it requires a process from temperature detection to adding and subtracting flames to adjust the temperature. In order to ensure that the mixing temperature mixing station does not produce waste, the operator should carefully observe the temperature change rate, predict the temperature change results in advance, and manually increase or decrease the flame or increase or decrease the feed amount to control the temperature changes so that the change results Do not exceed the specified range, thereby reducing or eliminating waste.
(2) Grading control of mixture:
The gradation of the mixture directly affects the performance of the pavement. If the gradation of the mixture is unreasonable, the pavement will suffer from some diseases such as larger or smaller void ratio, water permeability, rutting, etc., which will reduce the service life of the pavement and seriously affect the quality of the project. Therefore, the gradation control of the mixture is also one of the skills that the operator must possess.
Factors that affect the gradation of the mixture include: changes in raw material particle size, changes in the mixing station screen, measurement error range, etc.
The particle size of the raw materials directly affects the gradation of the mixture. When changes in the raw materials are found, the operator should cooperate with the laboratory to fine-tune the production mix ratio. The change of the hot material screen in the mixing station is an important factor affecting the gradation of the mixture. If the screen is clogged and the hot material is not adequately screened, the gradation will become thinner. If the screen is broken, damaged, leaked, or worn beyond the limit, , will make the mixture gradation coarser; the measurement error of the mixing station also directly affects the gradation. If the measurement error range is adjusted too large, the production mix ratio will deviate greatly from the target mix ratio, seriously affecting the quality of the mixture. If the measurement error range is adjusted too small, it will increase the measurement time and affect the output. It will also cause the measurement to frequently exceed the limit and affect the normal operation of the mixing station.
In short, the operator should pay close attention to the changes in raw materials, check the screen frequently, solve problems in a timely manner, and adjust the measuring range to the best condition according to the characteristics of the mixing station and other factors. Carefully consider other factors that affect gradation to ensure the mix ratio of the jet mill mixture.
(3) Control of the oil-stone ratio of the mixture:
The asphalt mixture's asphalt-stone ratio is determined by the gradation of mineral materials and the content of powder. It is the fundamental guarantee for the strength of the pavement and its performance. Too much or too little asphalt will cause different diseases on the pavement.
Therefore, strictly controlling the amount of asphalt is an important part of production control. Operators should pay attention to the following aspects during production:
During operation, try to adjust the error range of asphalt measurement as small as possible to achieve the best asphalt measurement; the amount of additional powder is also an important factor affecting the asphalt-stone ratio, so the measurement of powder must also be carefully controlled; according to the dust content of the fine aggregate, make reasonable adjustments The opening of the induced draft fan ensures that the dust content in the mixture is within the design range.