The brief discussion on the working principle, mixing control and troubleshooting of asphalt mixing plants
At present, the global highway construction industry has been greatly improved, the grades of highways are also constantly increasing, and there are increasingly higher requirements for quality. Therefore, when using asphalt pavement, the quality of the pavement must be guaranteed, and The quality of asphalt pavement is affected by the performance of the mixing equipment. In daily work, some faults often occur in intermittent mixing plants. Therefore, effective measures must be taken to deal with the faults so that the asphalt mixing plant can operate normally, thereby ensuring the quality of the asphalt pavement.
[1]. Working principle of asphalt mixing station
Asphalt mixture mixing equipment mainly includes two types, namely intermittent and continuous. At present, intermittent mixing equipment is often used in our country. When the central control room issues a command, the aggregates in the cold material bin will automatically enter the hot material bin, and then each material will be weighed, and then the materials will be placed in the mixing cylinder according to the specified proportion. Finally, the finished product is formed, the materials are unloaded onto the transport vehicle, and then put into use. This process is the working principle of the intermittent mixing plant. The intermittent asphalt mixing plant can effectively control the transportation and drying of aggregates, and even the transportation of asphalt.
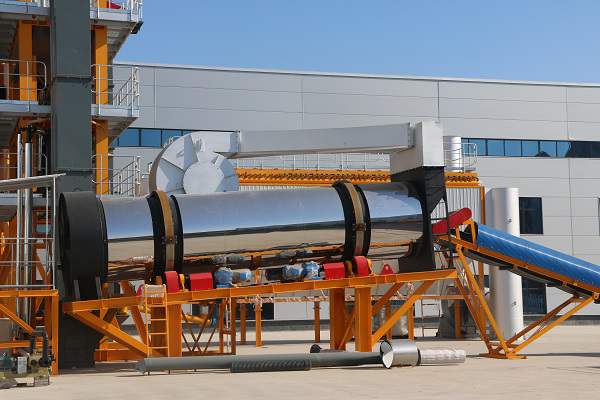
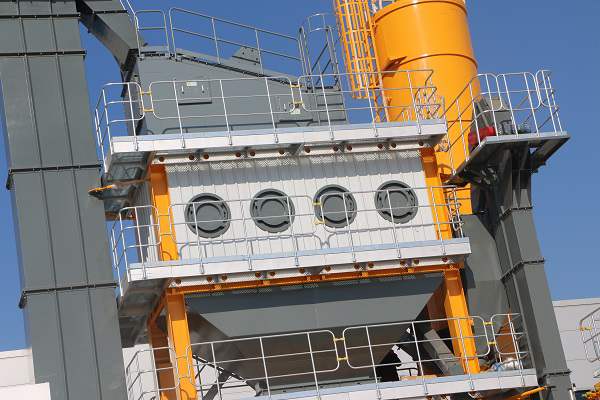
[2]. Asphalt mixing control
2.1 Control of mineral materials
During the construction process, the so-called coarse mineral material is gravel, and its particle size range is generally between 2.36mm and 25mm. The stability of the concrete structure is mainly directly related to the interlocking of the aggregate particles. At the same time, in order to be effective To resist displacement, friction force must be fully utilized. During the construction process, the coarse aggregate must be crushed into cubic particles.
2.2 Control of asphalt
Before using asphalt, various indicators must be inspected to ensure that the quality is qualified before it can be officially put into construction. When choosing the grade of asphalt, you must investigate the local climate. When the temperature is low, you should choose asphalt with a higher grade. This is mainly because asphalt with a high grade has a lower consistency and greater penetration. It will increase the crack resistance of asphalt pavement. During the construction process, the surface layer of the road needs to be relatively thin asphalt, and the middle and lower layers of the road should use relatively dense asphalt. This can not only enhance the crack resistance of the asphalt pavement, but also enhance its ability to resist rutting.
2.3 Control of fine aggregates
Fine aggregate generally refers to broken rock, and its particle size ranges from 0.075mm to 2.36mm. Before it is put into construction, it must be cleaned to ensure the cleanliness of the material.
2.4 Control of temperature
During the laying process, the temperature must be strictly controlled and operations must be carried out in accordance with relevant regulations to ensure the quality of the construction. When heating asphalt, it must be ensured that its temperature is between 150°C and 170°C, and the temperature of the mineral material must be lower than its temperature. The temperature of the mixture before leaving the factory should be controlled between 140°C and 155°C, and the paving temperature should be between 135°C and 150°C. During the entire process, the temperature must be monitored in real time. When the temperature exceeds the range, the temperature must be adjusted. It makes timely adjustments to ensure the quality of asphalt concrete.
2.5 Control of mix ratio
In order to control the proportion of ingredients, repeated tests must be carried out to determine the amount of asphalt used. The mineral materials must be heated, and the heated mineral materials must be sent to the outer cylinder and the inner silo. At the same time, other ingredients must be added and stirred thoroughly, and the mixture must be screened to achieve the desired mix ratio. The mixing time of the mixture generally exceeds 45 seconds, but cannot exceed 90 seconds, and it must be continuously inspected during the mixing process to ensure that various indicators meet the requirements.
[3]. Troubleshooting of asphalt mixing station
3.1 Troubleshooting of sensors and cold material conveying devices
During the normal operation of the asphalt mixing station, if the materials are not added according to regulations, it may cause the sensor to malfunction, thus affecting the signal transmission and inspection. When the variable speed belt stops, the variable speed belt motor may not work properly, and may even cause belt slippage and road deviation failure. Therefore, the belt must be inspected regularly. If during the inspection, the belt is found to be loose. The phenomenon must be dealt with in time to ensure that the device can operate normally.
3.2 Negative pressure troubleshooting
The atmospheric pressure inside the drying drum is the so-called negative pressure. Negative pressure is generally affected by two aspects, namely induced draft fans and blowers. Under the action of positive pressure, the dust in the drum may fly out from around the drum, which will have a great impact on the environment, so negative pressure must be controlled.
The abnormal sound of the mixer may be caused by the instantaneous overload of the mixer, so it must be reset in time. When the mixer arm and internal guard plate are damaged, they must be replaced to ensure that the mixer can mix normally.
3.3 The burner cannot ignite and burn normally
When there is a problem with the burner, the air conditioning compressor must first check the inside of the operating room to see if the ignition conditions are normal. If these conditions are normal, you need to check whether the fuel is sufficient or whether the fuel passage is blocked. When a problem is found , it is necessary to add fuel or clean the passage in time to ensure the normal operation of the burner.
[4] Conclusion
Ensuring the working quality of the asphalt mixing station can not only ensure the progress of the project, but also effectively reduce the project cost. Therefore, it is necessary to effectively control the asphalt mixing station. When a fault is discovered, it must be dealt with in a timely manner, so as to Ensure the quality of asphalt concrete and improve construction efficiency and economic benefits.