Treatment of the heavy oil combustion system failure in asphalt mixing station
An asphalt mixing station (hereinafter referred to as the mixing station) used by a certain unit uses diesel as fuel in production. As the market diesel price continues to rise, the operating cost of the equipment is getting higher and higher, and the efficiency is constantly decreasing. In order to reduce production costs, it is decided to use a low-priced, combustion-friendly and qualified special combustion oil (heavy oil for short) to replace diesel as fuel.
1. Fault phenomenon
During the use of heavy oil, the asphalt mixing equipment has black smoke from combustion, blackened recycled mineral powder, darkened combustion flames, and smelly hot aggregates, and the fuel oil consumption is large (7kg of heavy oil is required to produce 1t of finished material). After producing 3000t of finished material, the imported fuel high-pressure pump used was damaged. After disassembling the fuel high-pressure pump, it was found that its copper sleeve and screw were severely damaged. Through the analysis of the structure and materials of the pump, it was found that the copper sleeve and screw used in the pump are not suitable for use when burning heavy oil. After replacing the imported fuel high-pressure pump with a domestic fuel high-pressure pump, the phenomenon of burning black smoke still exists.
According to analysis, the black smoke is caused by incomplete combustion of the mechanical burner. There are three main reasons: first, the uneven mixing of air and oil; second, poor fuel atomization; and third, the flame is too long. Incomplete combustion will not only cause the residue to stick to the gap of the dust collector bag, hindering the separation of dust from the flue gas, but also make it difficult for the dust to fall off the bag, affecting the dust removal effect. In addition, the sulfur dioxide produced during the combustion process will also cause serious corrosion to the bag. In order to solve the problem of incomplete combustion of heavy oil, we have taken the following improvement measures.
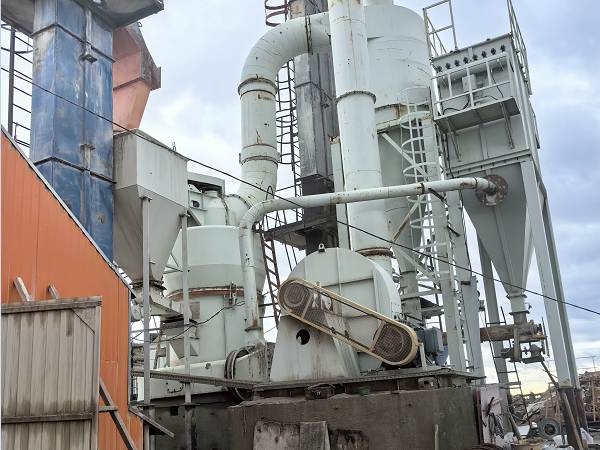

2. Improvement measures
(1) Control the viscosity of the oil
When the viscosity of heavy oil increases, the oil particles are not easy to disperse into fine droplets, which will produce poor atomization, resulting in black smoke from combustion. Therefore, the viscosity of the oil must be controlled.
(2) Increase the injection pressure of the burner
The function of the burner is to atomize the heavy oil into finer particles and inject them into the drum to mix with the air to form a good combustible mixture. Therefore, we increased the injection pressure of the burner, effectively improving the quality of the combustible mixture and improving the fuel conditions. (3) Adjust the air-oil ratio
Adjusting the air-oil ratio appropriately can make the fuel and air form a good mixture, avoiding incomplete combustion causing black smoke and increased fuel consumption. (4) Add a fuel filter device
Replace a new fuel high-pressure pump, keep the original circuit, pressure gauge, safety valve, stainless steel chain and other devices unchanged, and set a multi-stage filter device on some fuel pipelines to reduce impurities in the heavy oil and ensure full combustion.