What you want to know about the daily maintenance of asphalt mixing plants
Asphalt mixing equipment (asphalt concrete mixing equipment) all work in open-air sites, with heavy dust pollution. Many parts work in high temperatures of 140-160 degrees, and each shift lasts up to 12-14 hours. Therefore, the daily maintenance of the equipment is related to the normal operation and service life of the equipment. So how to do a good job in the daily maintenance of asphalt mixing station equipment?
Work before starting the asphalt mixing station
Before starting the machine, the scattered materials near the conveyor belt should be cleared; start the machine without load first, and then work with load after the motor is running normally; when the equipment is running with load, a special person should be assigned to track and inspect the equipment, adjust the belt in time, observe the operating status of the equipment, check whether there are any abnormal sounds and abnormal phenomena, and whether the exposed instrument display is working normally. If any abnormality is found, the cause should be found out and eliminated in time. After each shift, the equipment should be fully inspected and maintained; for high-temperature moving parts, grease should be added and replaced after each shift; clean the air filter element and gas-water separator filter element of the air compressor; check the oil level and oil quality of the air compressor lubricating oil; check the oil level and oil quality in the reducer; adjust the tightness of the belt and chain, and replace the belt and chain links when necessary; clean the dust in the dust collector and the debris and waste scattered on the site to keep the site clean. Problems found during inspections during work should be thoroughly eliminated after the shift, and operation records should be kept. In order to grasp the full use of the equipment.
Maintenance work requires persistence. It is not a job that can be done overnight. It must be done in a timely and appropriate manner to extend the life of the equipment and maintain its production capacity.
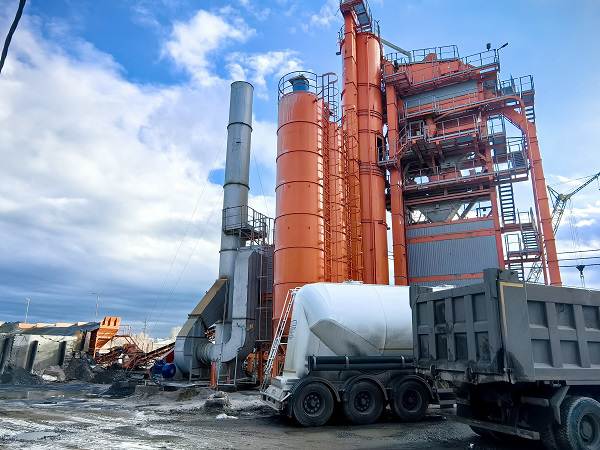
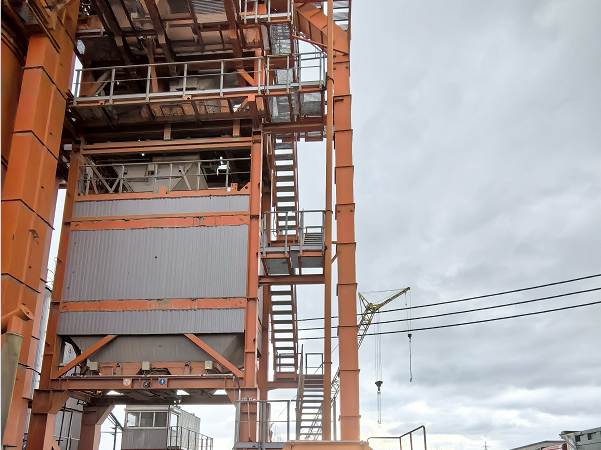
Asphalt mixing plant three diligence and three inspection work
Asphalt mixing equipment is a mechatronic equipment, which is relatively complex and has a harsh operating environment. To ensure that the equipment has fewer failures, the crew must be "three diligence": diligent inspection, diligent maintenance, and diligent repair. "Three inspections": inspection before equipment startup, inspection during operation, and inspection after shutdown. Do a good job in routine maintenance and regular maintenance of equipment, do a good job in "cross" operations (cleaning, lubrication, adjustment, tightening, anti-corrosion), manage, use and maintain the equipment well, ensure the integrity rate and utilization rate, and maintain the parts that need maintenance in strict accordance with the equipment maintenance requirements.
Do a good job in daily maintenance work and maintain it in strict accordance with the equipment maintenance requirements. During production, you must observe and listen, and immediately shut down for maintenance when abnormal conditions occur. Do not operate with illness. It is strictly forbidden to carry out maintenance and debugging work when the equipment is running. Special personnel should be arranged to monitor key parts. Make good reserves for vulnerable parts and study the causes of their damage. Carefully fill in the operation record, mainly record what kind of fault occurred, what phenomenon occurred, how to analyze and eliminate it, and how to prevent it. The operation record has a good reference value as a hand material. During the production period, you must be calm and avoid being impatient. As long as you master the rules and think patiently, any fault can be well solved.
Daily routine maintenance of asphalt mixing plant
1. Lubricate the equipment according to the lubrication list.
2. Check the vibrating screen according to the maintenance manual.
3. Check whether the gas pipeline is leaking.
4. Blockage of large particle overflow pipeline.
5. Dust in the control room. Excessive dust will affect the electrical equipment.
6. After stopping the equipment, clean the discharge door of the mixing tank.
7. Check and tighten all bolts and nuts.
8. Check the lubrication of the screw conveyor shaft seal and necessary calibration.
9. Check the lubrication of the mixing drive gear through the observation hole and add lubricating oil as appropriate
Weekly inspection (every 50-60 hours)
1. Lubricate the equipment according to the lubrication list.
2. Check all conveyor belts for wear and damage, and repair or replace if necessary.
3. For the blades, check the gearbox oil level and inject the corresponding lubricant if necessary.
4. Check the tension of all V-belt drives and adjust if necessary.
5. Check the tightness of the hot material elevator bucket bolts and move the adjustment grid to facilitate the entry of hot aggregate into the screen box.
6. Check the chain and head and tail shaft sprockets or driving wheels of the hot material elevator and replace them if necessary.
7. Check whether the induced draft fan is clogged with dust - too much dust can cause violent vibration and abnormal bearing wear.
8. Check all gearboxes and add the lubricant recommended in the manual when necessary.
9. Check the connection parts and accessories of the tension sensor.
10. Check the tightness and wear of the screen and replace it if necessary.
11. Check the gap of the feed hopper cut-off switch (if installed).
12. Check all wire ropes for debonding and wear, check the top limit switch and proximity switch.
13. Check the cleanliness of the stone powder weighing hopper outlet.
14. Lubrication of the drive bearing of the ore trolley (if installed), the bearings of the winch gear and the ore car door.
15. The return valve of the primary dust collector.
16. The wear of the scraper plate inside the drying drum, the hinge, pin, lotus wheel (chain drive) of the drying drum drive chain, the adjustment and wear of the driving wheel coupling, support wheel and thrust wheel of the drying drum (friction drive).
17. The wear of the mixing cylinder blades, mixing arms, and shaft seals, if necessary, adjust or replace.
18. The blockage of the asphalt spray pipe (the sealing condition of the self-flowing inspection door)
19. Check the oil level in the lubrication cup of the gas system and fill it up if necessary.
Monthly inspection and maintenance (every 200-250 operating hours)
1. Lubricate the equipment according to the lubrication list.
2. Check the tightness and wear of the chain, hopper and sprocket of the hot material elevator.
3. Replace the sealing packing of the powder screw conveyor.
4. Clean the impeller of the induced draft fan, check for rust, and check the tightness of the foot bolts.
5. Check the wear of the thermometer (if installed)
6. The wear of the hot aggregate silo level indicator device.
7. Use a high-precision temperature indicator to monitor the accuracy of the thermometer and thermocouple on site.
8. Check the scraper of the drying drum and replace the scraper that is severely worn.
9. Check the burner according to the operating instructions of the burner.
10. Check the leakage of the asphalt three-way valve.
Inspection and maintenance every three months (every 600-750 operating hours).
1. Lubricate the equipment according to the lubrication list.
2. Check the wear of the hot hopper and the discharge door.
3. Check the damage of the screen support spring and bearing seat, and adjust according to the geotextile instructions if necessary.
Inspection and maintenance every six months
1. Lubricate the equipment according to the lubrication list.
2. Replace the mixing cylinder blades and bearing grease.
3. Lubricate and maintain the whole machine motor.
Annual inspection and maintenance
1. Lubricate the equipment according to the lubrication list.
2. Clean the gear box and gear shaft device and fill them with the corresponding lubricating oil.