In the process of highway construction projects, road construction machinery often causes many problems due to improper use, so the progress of the project has to be suspended, which seriously affects the completion of the construction project. For example, the problem of the reversing valve of the asphalt mixer plant.
The faults of the reversing valve of the asphalt mixer plant in road construction machinery are not complicated. Common ones are untimely reversing, gas leakage, electromagnetic pilot valve failure, etc. The corresponding causes and solutions are of course different. For the reversing valve to not change direction in time, it is generally caused by poor lubrication, the spring is stuck or damaged, oil dirt or impurities get stuck in the sliding part, etc. For this, it is necessary to check the status of the lubricator and the quality of the lubricating oil. Viscosity, if necessary, the lubricant or other parts can be replaced.
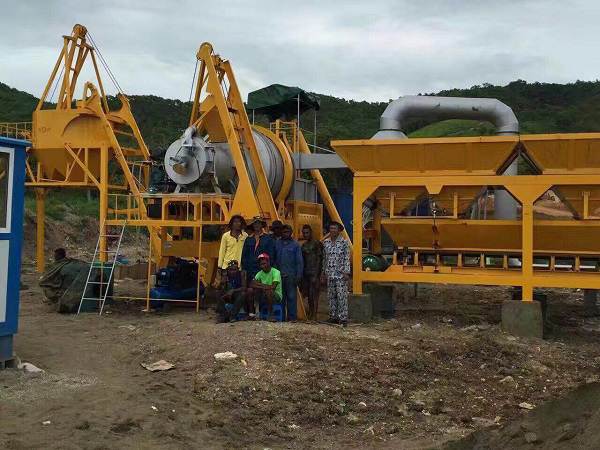
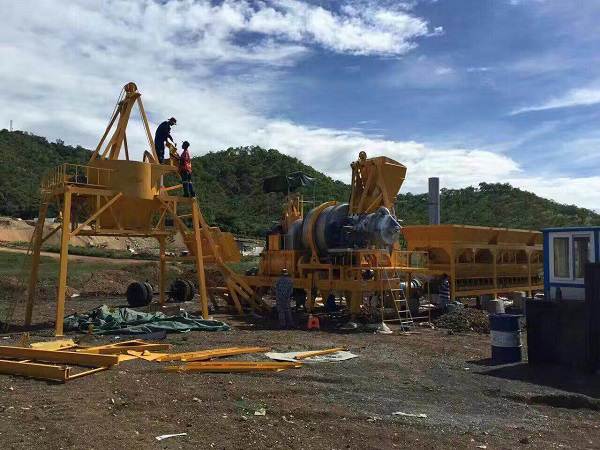
After long-term use, the reversing valve is prone to wear of the valve core sealing ring, damage to the valve stem and valve seat, resulting in gas leakage in the valve. At this time, the sealing ring, valve stem and valve seat should be replaced, or the reversing valve should be replaced directly. In order to reduce the failure rate of asphalt mixers, maintenance must be strengthened on a daily basis.
Once the road construction machinery breaks down, it can easily affect the progress of the project, or even stop the progress of the project in serious cases. However, due to the influence of work content and environmental factors, asphalt mixing equipment will inevitably suffer losses during operation. In order to reduce losses and extend the service life of the equipment, we must do a good job in maintenance.
Check whether the bolts of the vibration motor are loose; check whether the bolts of each component of the batching station are loose; check whether each roller is stuck/not rotating; check whether the belt is deflected; check the oil level and leakage, and replace the damaged seal if necessary parts and add grease; clean the ventilation holes; apply grease on the belt conveyor tensioning screw.
Check whether the bolts of each component of the dust collector are loose; check whether each cylinder operates normally; check whether each cylinder operates normally and whether there is leakage in each air path; check whether there is any abnormal noise in the induced draft fan, whether the belt is appropriately tight, and whether the adjustment damper is flexible. The machine can be shut down regularly during operation to minimize the loss of the vibrating screen.